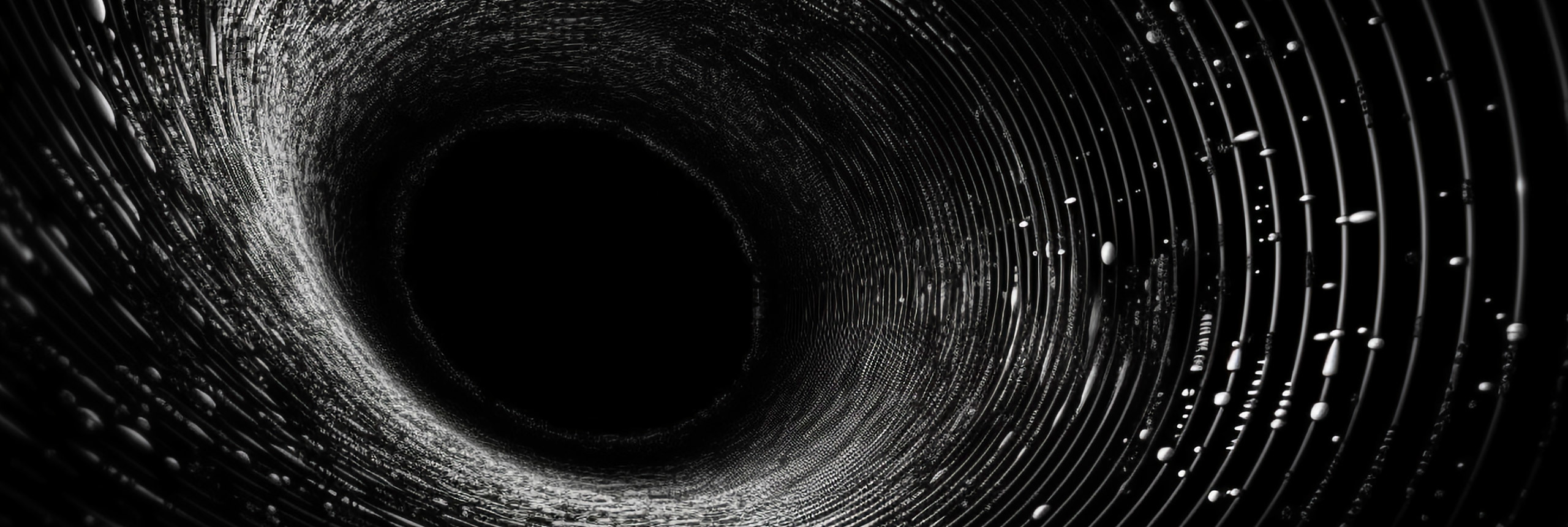
Comparison between aluminum-magnesium manganese alloy roof panel and color steel plate
The use of metal sheets as roofing materials has been hundreds of years of history, a large number of metal materials used as roofing materials mainly because of the rapid development of the world's metallurgical industry since the 60's, able to produce a variety of specifications and to meet the quality requirements of the metal sheet, and reduce the cost.
Metal roofing materials are mainly galvanized steel, stainless steel, aluminum alloy plate, copper, zinc-copper titanium composite plate and pure titanium plate. The advantages of metal sheet roofing are simple and fast construction, good waterproof performance and reusability. In addition to being resistant to the highest and lowest temperatures that the earth's climate can produce, it is seldom affected by the stresses generated by climate and roof deformation when used as a roofing material, and can be painted in a variety of colors according to the situation.
Aluminum-magnesium-manganese alloy sheet roof/curtain wall system mainly uses 3000 series of aluminum-manganese (aluminum-manganese-magnesium) alloy, 3000 series of aluminum-manganese alloy elongation, hardness, tensile strength, yield strength and other indexes are very suitable for the roofing of the rolled edge, rolling pressure equipment processing. Therefore, it is widely used in the roof/wall system and other building exterior maintenance projects, and with a variety of painting systems and painting processes to make the building appearance become colorful, but also increase the corrosion resistance of the aluminum alloy itself.
The minimum thickness of the aluminum material selected for roofing is 0.7mm. When the thickness of aluminum is 1mm, its weight is 2.7kg/square meter, and when the thickness is 0.7mm, the mass of aluminum is 1.89kg/square meter. The length of the coil is unlimited.
Its main characteristics are: density of 2.7, melting point of 658, temperature of 20 ~ 100 degrees when the linear expansion coefficient of 0.0000023, breaking load factor of 8 ~ 12 kg / mm2 (according to the hardness of the material varies), elongation of 10 ~ 40%, the thickness of 0.7 ~ 1.2mm, when the thickness of aluminum corrugated sheet can be reduced to 0.6mm, the fixing method in addition to the coil Edge bite, rivets, but also can be used in the form of welding.
A durability comparison: aluminum-magnesium-manganese alloy can form aluminum oxide film with the atmosphere to prevent further corrosion, used in civil construction generally have 15-20 years of coating warranty. Building design service life of more than 50 years. General guarantee 25 years of product warranty; color steel plate in the humid air and rain, snow and water erosion is easy to corrode and rust to fracture accidents, especially rivets, seams of the parts.
Second, weight comparison: aluminum-magnesium manganese alloy weight light (density of 2730 kg / square meter); color steel plate weight is heavier (density of 7850 kg / square meter)
Third, the strength and steel contrast: aluminum alloy of aluminum-magnesium-manganese alloy has magnesium, manganese content, so it has a certain strength and stiffness. But the internal stress and hardening of aluminum alloy plate, strength, etc. There is no obvious yield point, not as good as color steel; color steel plate strength and stiffness is better, not easy to deformation, etc..
Fourth, appearance against: aluminum-magnesium-manganese alloy can be divided into non-painted (hammered, embossed, pre-passivated alumina surface treatment, etc.) and painted (PVDF, SMP, PE, etc.); color steel plate can be divided into non-painted (hot-plated aluminum-zinc alloy steel strip: light plate) and painted (PVDF, SMP, PE, HDP, etc.).
Fifth, lightning performance: aluminum-magnesium manganese alloy thickness is generally 0.7mm and 0.9mm, can be used directly as a lightning connector (national norms, "building lightning protection design norms" GB50057), to avoid perforation of the roof; color steel plate is generally 0.5mm thick aluminum-zinc-plated and zinc-plated steel sheet, can not be used directly as a lightning connector, you need to additionally set up a lightning connector (such as lightning rods).
Sixth, safety and fire: aluminum-magnesium-manganese alloy melting point is low (660 degrees Celsius). High temperature performance is poor, 150 degrees above the rapid loss of strength. When a fire occurs, the roof is easy to be burned through, so that the fire spreads outward, not inward lateral spread, help the fireman from the top of the stretch fire hose fire; Color steel plate steel melting point is high (1515 degrees Celsius).
Seven, molding: aluminum-magnesium-manganese alloy has good weldability, high plasticity, low-temperature environment, the strength and ductility of the aluminum alloy has improved, with good low-temperature working performance; color steel plate steel at low temperatures are prone to cold brittle.
Eight, cost-effective: aluminum-magnesium-manganese alloy cost-effective: light, waterproof, easy to bend arc, three-dimensional visual effect; color steel plate cost-effective lower: heavy, waterproof a little worse, steel strong bending arc a little worse, poor artistic effect.
RELATED INFORMATION
Shandong Taihui New Material Science and Technology Co., Ltd. was awarded the Digital Outbound Global Excellent Partner
Introduction to the advantages and uses of fluorocarbon coated colored aluminum coil
Coated aluminum coil, color coated aluminum coil, 3004 aluminum-magnesium-manganese color coated aluminum coil, color coated aluminum coil aluminum strip, color coated aluminum strip, color aluminum strip and so on.
Company news
-
Shandong Taihui New Material Science and Technology Co., Ltd. was awarded the Digital Outbound Global Excellent Partner
Time:2025-02-20
-
Introduction to the advantages and uses of fluorocarbon coated colored aluminum coil
Time:2024-01-23
-
What are the reasons affecting the service life of nano anti-corrosion heat insulation boards?
Time:2024-01-23
-
How to use the nano anti-corrosion heat insulation board and application areas
Time:2024-01-23
-
What is the detailed construction method of nano anti-corrosion heat insulation boards
Time:2024-01-23
-
Teach you how to distinguish between good and bad quality of color coated sheet?
Time:2024-01-23
-
Color coated panels - a wide range of applications
Time:2024-01-23
Industry news
-
Why chrome-free switching for color coated plate production
Time:2024-01-23
-
Fire danger and preventive measures of color steel plate building
Time:2024-01-23
-
Comparison between aluminum-magnesium manganese alloy roof panel and color steel plate
Time:2024-01-23
-
Color steel plate purification decoration project construction methods and requirements
Time:2024-01-23